Shift-Handoff Report Generation
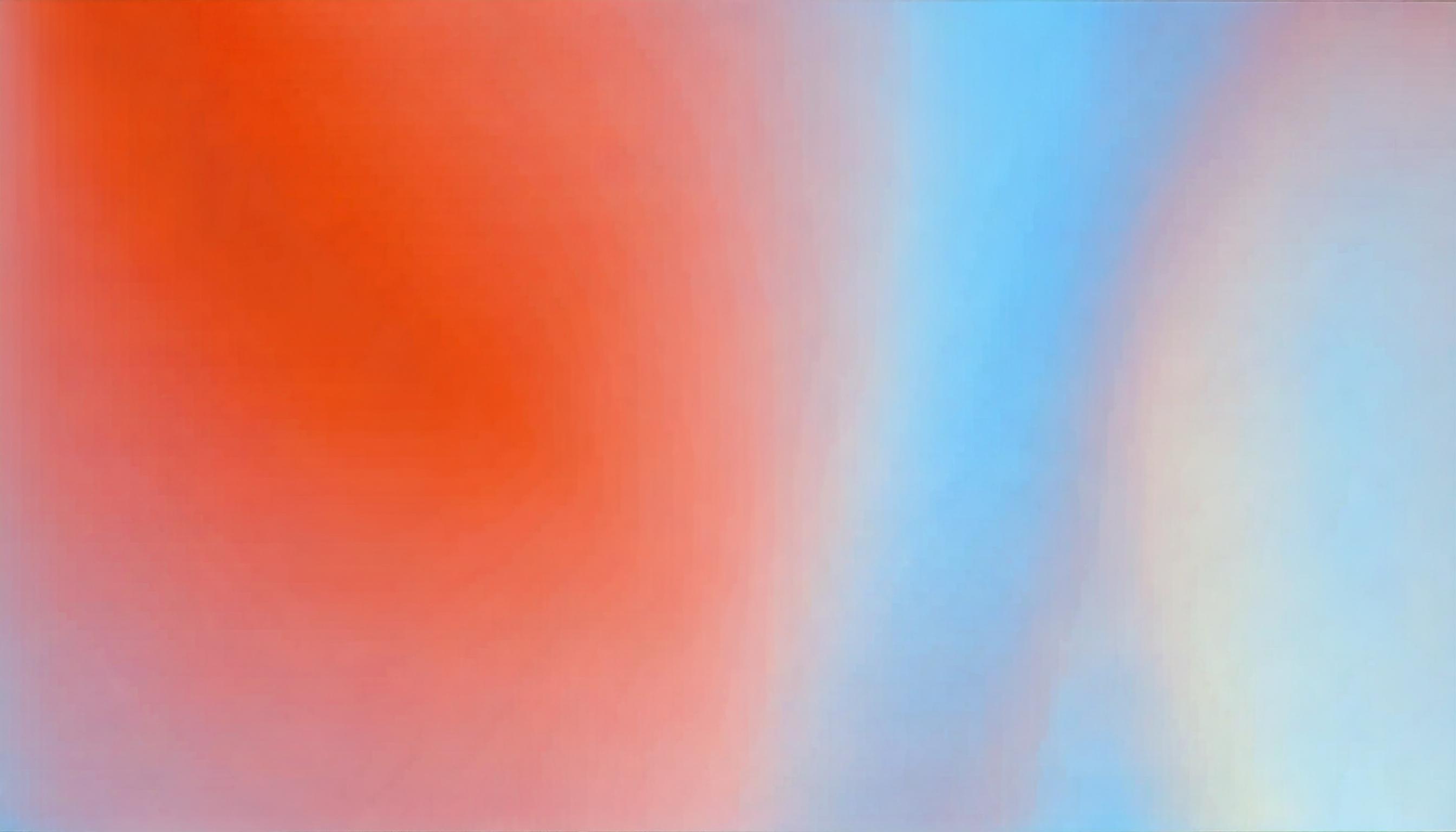
How RAG systems could be used to automate periodic reporting in the oil and gas industry.
Improving Shift-Handoff Reports in Oil and Gas Operations: A Practical Approach
In the demanding world of oil and gas operations, where precision and safety are crucial, streamlining processes can lead to significant improvements in productivity and risk management. The shift-handoff reporting process, a critical yet often time-consuming task, impacts operational continuity and safety. This article explores how technology and process optimization could transform this essential function, potentially reducing report generation time from hours to minutes while enhancing the quality and utility of the information shared.
Traditionally, oil and gas companies face a challenging task at every shift change: compiling comprehensive reports on the status of ongoing operations, equipment conditions, and safety concerns. This process typically involves:
- Manual data collection from various sources (e.g., equipment readouts, supervisory control and data acquisition (SCADA) systems, field observations)
- Handwritten or basic digital entry of operational parameters and incidents
- Verbal communication of critical information during shift changes
- Time-consuming review and synthesis of information by incoming shift personnel
This manual approach, while thorough, has several inefficiencies. Field operators and supervisors often spend a significant portion of their shift compiling and communicating this information, taking valuable time away from active monitoring and decision-making. The opportunity cost is substantial—highly trained professionals spending considerable time on data entry rather than value-added analysis and proactive operational management.
Envisioning a Technological Solution
Consider a world where this process is automated, using industrial IoT and artificial intelligence. Here's how such a system could work:
-
Automated Data Aggregation: By developing robust APIs and data pipelines, it's possible to create a system that automatically pulls relevant information from various operational data sources. This could include real-time equipment performance metrics, historical operational data, safety incident logs, and unstructured data from field observations.
-
Dynamic Report Generation: A report generation engine could compile standardized shift-handoff reports based on predefined templates and the processed data inputs. This system could use language models to draft initial analyses, allowing human operators to focus on higher-level insights and decision-making.
-
Streamlined Standard Operating Procedures (SOPs): Along with technological solutions, companies could optimize their internal processes. This might involve redefining operator roles, establishing clear data governance policies, and implementing efficient methodologies for report review and dissemination.
The implementation of such a system could yield significant results:
-
Improved Time Efficiency: Report generation time could be reduced from hours to minutes—a substantial decrease. This time savings could be redirected towards more strategic activities, such as proactive equipment maintenance, safety inspections, or advanced operational planning.
-
Better Accuracy and Consistency: By reducing manual data entry, the risk of human error could be lowered. Additionally, standardized report templates would ensure consistency across different shifts and operational areas, improving the overall quality of the company's operational intelligence.
-
Enhanced Analytical Capabilities: With less time spent on data compilation, operators could focus on developing more effective operational strategies, conducting scenario analyses, and providing more insightful commentary on emerging trends or potential issues.
-
Increased Scalability and Flexibility: An automated system would make expanding operations or integrating new equipment more manageable. The company could adapt to changing operational conditions or regulatory demands without proportionally increasing workload or headcount.
-
Operational Excellence: In an industry where safety and efficiency are crucial, the ability to generate timely, in-depth operational reports could significantly improve a company's operational performance. This could lead to increased productivity and improved stakeholder confidence.
The Broader Implications: Potential for Industry-Wide Change
The effects of such an innovation could extend beyond operational efficiency:
-
Safety Improvement: Comprehensive and accurate information transfer between shifts could reduce the risk of safety incidents due to miscommunication or oversight.
-
Talent Management: By reducing tedious work associated with shift reporting, companies might find it easier to attract and retain skilled personnel. The role of field operators could evolve to focus more on developing strategic insights and proactive problem-solving skills.
-
New Operational Insights: With structured data readily available, companies could develop data-driven approaches to operational optimization. This might include predictive maintenance schedules, real-time performance optimization, or AI-assisted operational decision support systems.
-
Improved Regulatory Compliance: A standardized, auditable process for shift-handoff reporting could streamline compliance efforts and reduce the risk of regulatory infractions.
The approach outlined here represents more than just a technological upgrade—it's a practical reimagining of how operational continuity is maintained in the modern oil and gas industry. By leveraging technology and optimizing human capital, companies have the opportunity to improve their operational efficiency and enhance the safety and reliability of their operations.
As the oil and gas industry continues to evolve in response to technological advancements and increasing demands for safety and environmental responsibility, companies that embrace practical innovation in their core processes will be well-positioned to succeed. The automation of shift-handoff reporting is one example of how traditional operational functions can be improved, indicating a path towards a more efficient, insightful, and competitive future for the industry.